BIOPLASTICS
Timeline
Testing Procedures

Innovators
European Bioplastics
Located in Berlin, Germany, European Bioplastics is a European association consisting of 7 board members that are representatives of other companies working with European Bioplastics like EU institutions. They also work with decision makers to create a foundational system for bioplastics to flourish and thrive in. Every year they would hold an annual conference bringing decision makers and stakeholders together to inform them of the advancements and difference bioplastics are making in the industry.
Furthermore, they try to inform businesses, brands, consumers, policy makers, media, and the public what bioplastics has to offer through their publications, papers, market data, newsletter, and news updates. [I.1]
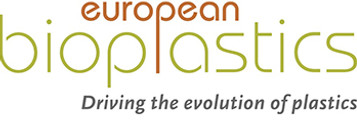

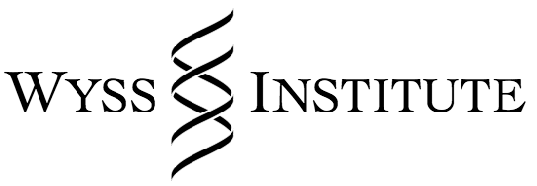
Harvard University
A team of researchers at Harvard’s Wyss Institute for Biologically Inspired Engineering led by Dr. Fellow Javier Fernandez and Dr. Don Ingber have developed a new bioplastic called Shrilk from chitin in shrimp shells and from a small amount of fibroin protein from silk! Shrilk is such a tough material that it can be used to create implantable foams, films and scaffolds, tissue engineering, and in many regenerative medicine applications. This can be done through traditional casting or injection molding manufacturing techniques.
Also, the new bioplastic can easily biodegrade in the soil within 2 weeks, helping to enable new plant growth by leaving nutrients in the soil. [I.2]
Gert-Jan Gruter
Gert-Jan Gruter, a Dutch chemist and his team at Amsterdam-based chemicals company Avantium developed a biodegradable and bio-based plastic called polyethylene furanoate (PEF). He and his team did so by processing the sugar in plant starch into the building block of PEF, furandicarboxylic acid (FDCA). The new bioplastic is fully recyclable and it lowers carbon dioxide emissions up to 70%. For his work, Gert-Jan Gruter was nominated at the European Inventor Award 2017 for the European Patent Office (EPO) prize.
As of now, Avantium is cooperating with food and bottle companies to help bring about PEF into the market and production and hopefully by 2021. And a way they are making this possible is by constructing an industrial-scale plant in Antwerp, Belgium just for PEF. [I.3]


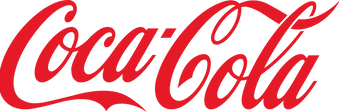

Coca-Cola
On June 3, 2015, Coca-Cola announced the first PET plastic bottle made partly from renewable plant based materials that was fully recyclable! Researchers and inventors at Coca-Cola came up with what they would later call, “Plantbottle” by using patented technology which extracted the sugars from plants (sugarcane) to manufacture PET.
Their goal was to stay away from the use of fossil based materials and switch over to renewable resources. Therefore, they could reduce their impact on the environment by lowering their carbon footprint compared to traditional PET. [I.4]
Iowa State
University
Iowa State University and Washington State University is collaborating with each other to set up the Center for Bioplastics and Biocomposites (CB2), a National Science Foundation Industry & University Cooperative Research Center (I/UCRC). The goal of the research institution is to help initiate the development of bioplastics by supporting the use of renewable resources and by working with other industrial and university partners to study the areas pertaining to bioplastics. Currently, their attentions are being driven towards areas like synthesis and compounding of bioplastics, biocomposites, bio-based products, and medical applications. [I.5]
Washington State
​



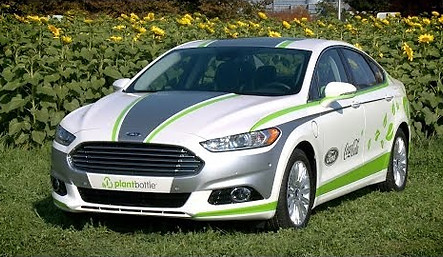
Ford
“Since 2008, [Ford has] used soy foam as a replacement for petroleum oil in the seat cushions and headrests of our iconic Mustang” (Mielewski). But now, Ford is making an effort to team up with Jose Cuervo, a Tequila company in Mexico to design newer and more advanced cars out of agave plants. Through the tequila production process, they can take agave which is the byproduct of the process and implement it into their vehicles. Because of this, it allows for vehicles to have more durable and lighter parts. Furthermore, Ford does not have to depend greatly on petrochemical for vehicle production, which lowers the impact it has on the environment. [I.6]